Project Information
Title of the project: | Dirigeo 2 – Design and generation of sealing shaft counter-surfaces using machining processes with geometrically defined cutting edges |
Duration: | 01/2025 – 12/2026 |
Funding programme: | Individual research grant |
Project execution organisation: | Deutsche Forschungsgemeinschaft (German Research Foundation) |
Project leader: | Prof. Dr.-Ing. Andreas Schubert |
Staff: | |
Project partner: | Chair of Machine Elements, Gears and Tribology (RPTU Kaiserslautern-Landau) |
Abstract: | For the sealing of shaft feedthroughs in pressure-free areas or sections with minor pressure difference typically radial shafts seals (RSS) are applied. However, the frictional torque of RSS is very high compared to other machine elements such as roller bearings. For example, a commercially available RSS with a diameter of 80 mm causes a frictional torque of 0.4 N m - 0.8 N m resulting in corresponding wear of the machine element. Therefore, the objective of the project is to reduce the friction and wear of RSS by a function-oriented modification of the turning process for the production of the shaft counter-surfaces (SCS). In this context, the influence of deterministic microstructures generated by hard turning on the hydrodynamic properties of the RSS in sealing contact is investigated. Hard turning of SCS is characterised by its high profitability compared to grinding, but can only be used to a limited extent due to the twist-induced conveying effect. However, a significant reduction of the conveying cross-section is only possible within narrow boundaries, as SCS with very low surface roughness values (Ra < 0.2 µm) can cause a break of the hydrodynamic lubricating film due to the disruption of the lubricant supply, resulting in thermal damage to the sealing edge. However, the generation of microstructured SCS by means of a two-stage turning process exploits the potential of very small conveying cross-sections, as the resulting microstructures maintain the lubricating film through their hydrodynamic pressure and reservoir effect. Thus, a reduction of friction and SCS wear are obtained. In a first process step (stage 1), the tool kinematics during external longitudinal turning is superimposed with a high-frequency ultrasonic oscillation perpendicular to the workpiece surface. The vibration of the tool creates a micro-structured surface which exhibits a sinusoidal profile in the cutting direction. In the second process step (stage 2), machining is carried out without the superimposition of an ultrasonic vibration, whereby the depth of cut is selected to be smaller than the microstructure depth generated by stage 1. The resulting microstructures in the form of calottes can be varied in terms of their size (width, length), spacing, and depth. The overall scientific objective of the research project is to gain a profound understanding of the interactions between microstructure geometry, fluid and RSS occurring in sealing contact. For this, machining and test bench experiments as well as computer-aided process and hydrodynamic simulation are used. On this basis, ultrasonic vibration-superimposed, two-stage hard turning can be established as a machining strategy in the production of hardened SCS. Additionally, the application potential of the resulting microstructures can be validated with regard to their functional behaviour in radial shaft seals. |
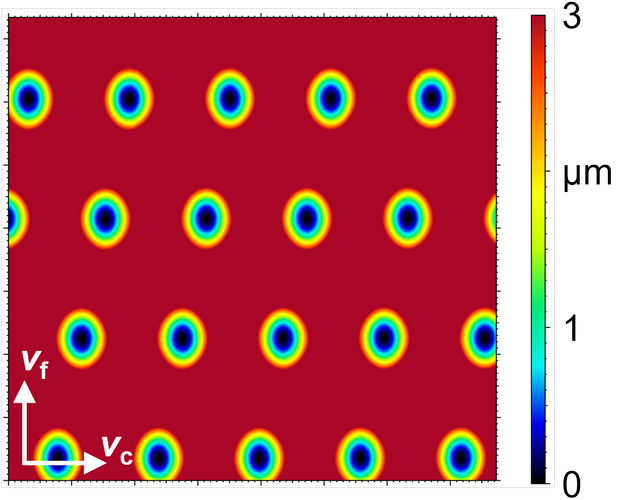
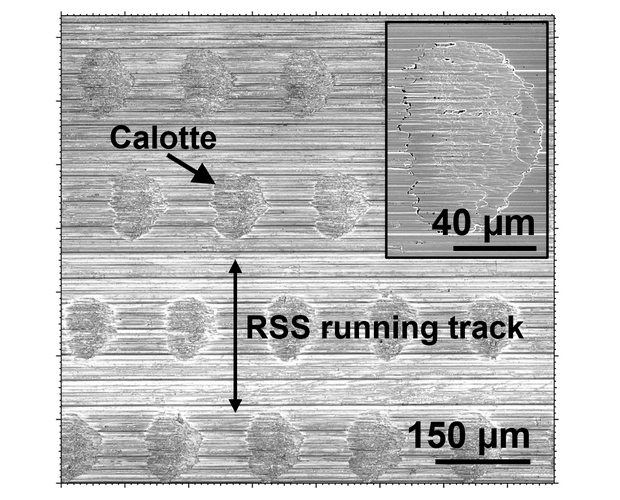
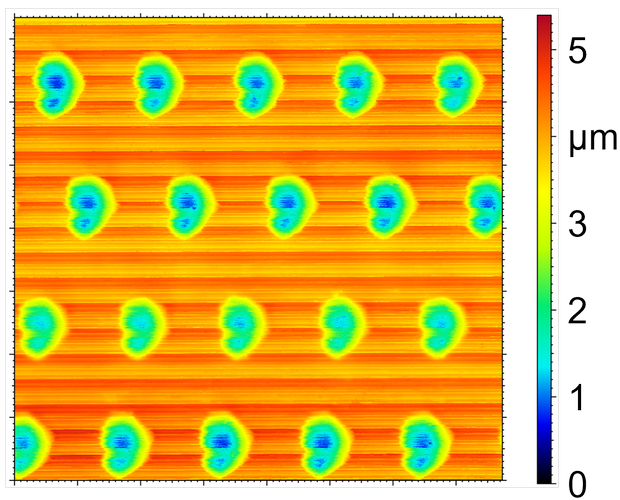