Projektinformationen
Titel des Projektes: | Dirigeo 2 – Auslegung und Erzeugung von Dichtringgegenlaufflächen mit Verfahren mit geometrisch bestimmten Schneiden |
Laufzeit: | 01/2025 – 12/2026 |
Förderprogramm: | Sachbeihilfe |
Projektträger: | Deutsche Forschungsgemeinschaft |
Projektleiter: | Prof. Dr.-Ing. Andreas Schubert |
Mitarbeiter: | |
Projektpartner: | Lehrstuhl für Maschinenelemente, Getriebe und Tribologie (RPTU Kaiserslautern-Landau) |
Zusammenfassung: | Zur Abdichtung von Wellendurchführungen im drucklosen Betrieb oder bei geringem Druckunterschied kommen überwiegend Radialwellendichtringe (RWDRs) zum Einsatz. Das Reibmoment von RWDRs ist im Vergleich zu anderen Maschinenelementen wie Wälzlagern jedoch sehr hoch. So verursacht beispielsweise ein handelsüblicher RWDR mit einem Durchmesser von 80 mm ein Reibmoment von 0,4 Nm bis 0,8 Nm, was auch einen entsprechenden Verschleiß dieses Maschinenelements nach sich zieht. Ziel des Projekts ist daher eine Verringerung der Reibung sowie des Verschleißes von RWDRs durch eine funktionsorientierte Modifikation des Drehprozesses zur Fertigung von Dichtringgegenlaufflächen (DRGFs). In diesem Zusammenhang steht der Einfluss von beim Hartdrehen gezielt eingebrachten, deterministischen Mikrostrukturen auf die hydrodynamischen Eigenschaften des RWDRs im Dichtkontakt im Fokus. Das Hartdrehen der DRGFs zeichnet sich gegenüber dem Schleifen vor allem durch seine höhere Wirtschaftlichkeit aus, ist jedoch wegen der drallinduzierten Förderwirkung nur eingeschränkt nutzbar. Eine deutliche Reduzierung des Förderquerschnitts ist lediglich innerhalb enger Grenzen möglich, da es bei DRGFs mit sehr geringen Rauheiten (Ra < 0,2 µm) aufgrund der Störung der Schmiermittelzufuhr zu einem Abriss des hydrodynamischen Schmierfilms und somit zu einer thermischen Schädigung der Dichtkante kommen kann. Die Erzeugung mikrostrukturierter DRGFs mittels einer zweistufigen Drehbearbeitung erschließt dagegen das Potenzial sehr kleiner Förderquerschnitte, da die resultierenden Mikrostrukturen durch ihre hydrodynamische Druck- und Reservoirwirkung den Schmierfilm aufrechterhalten und somit die Reibung sowie den Verschleiß der DRGFs reduzieren. Dafür wird in einem ersten Prozessschritt (Stufe 1) die Werkzeugkinematik beim Außenlängsdrehen mit einer hochfrequenten Ultraschallschwingung senkrecht zur Werkstückoberfläche überlagert. Die Schwingung des Werkzeugs erzeugt dabei eine mikrostrukturierte Oberfläche, welche in Schnittrichtung ein Sinusprofil aufweist. Im zweiten Prozessschritt (Stufe 2) erfolgt eine Bearbeitung ohne Ultraschallschwingung, wobei die Schnitttiefe kleiner gewählt wird als die durch Stufe 1 erzeugte Mikrostrukturtiefe. Die resultierenden Mikrostrukturen in Form von Kalotten können hinsichtlich ihrer Größe (Breite, Länge), ihres Abstands und ihrer Tiefe gezielt variiert werden. Das übergeordnete wissenschaftliche Ziel des Forschungsvorhabens besteht in der Erlangung eines tiefgründigen Verständnisses für die im Dichtkontakt auftretenden Wechselwirkungen zwischen Mikrostrukturgeometrie, Fluid und RWDR auf der Basis von Zerspanungs- und Prüfstandsversuchen sowie computergestützter Prozess- bzw. Hydrodynamik-Simulation. Auf dieser Grundlage kann das ultraschallschwingungsüberlagerte, zweistufige Hartdrehen als Bearbeitungsstrategie im Rahmen der Fertigung gehärteter DRGFs etabliert und das Anwendungspotenzial der resultierenden Mikrostrukturen bzgl. ihres funktionalen Verhaltens in Radialwellendichtungen validiert werden. |
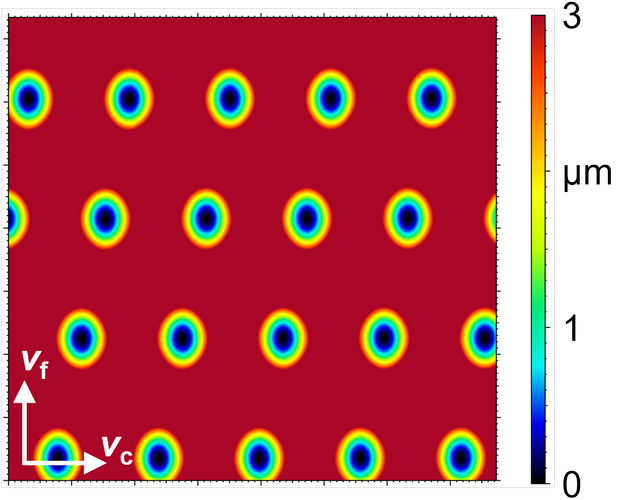
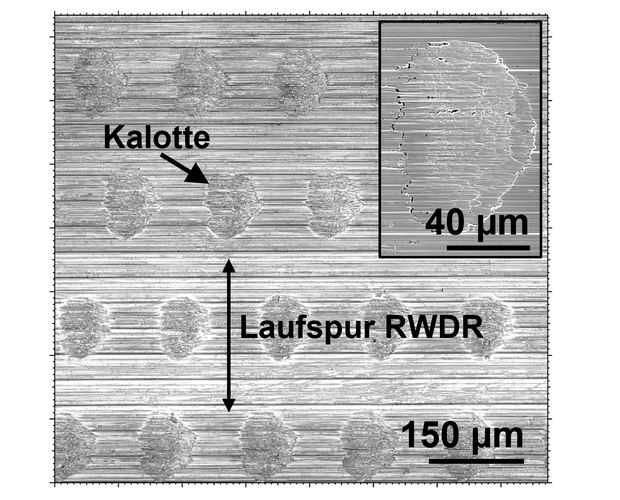
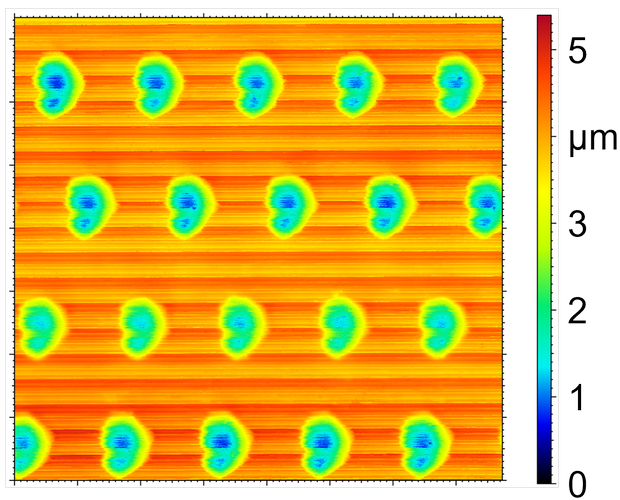